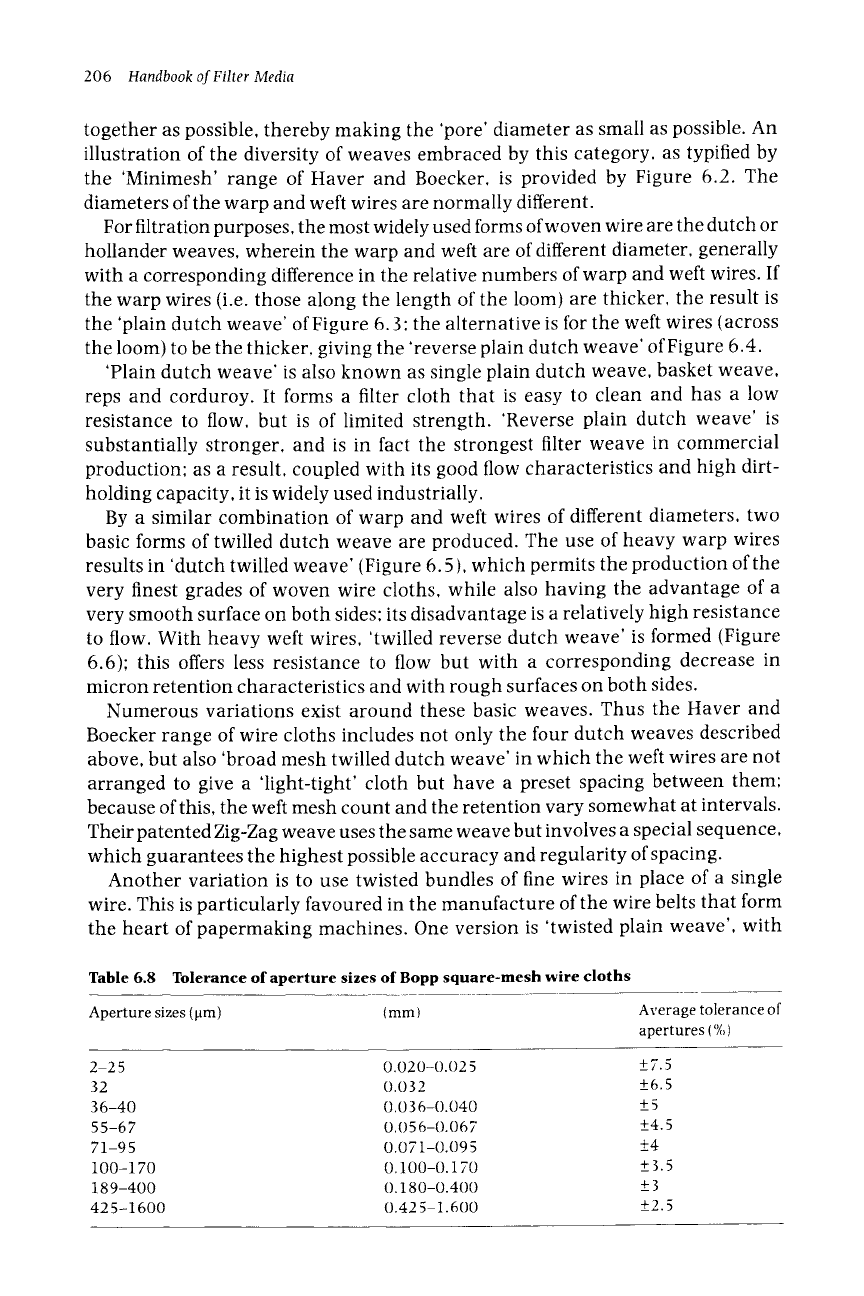
206
Handbook of Filter Media
together as possible, thereby making the 'pore' diameter as small as possible. An
illustration of the diversity of weaves embraced by this category, as typified by
the 'Minimesh' range of Hayer and Boecker, is provided by Figure 6.2. The
diameters of the warp and weft wires are normally different.
For filtration purposes, the most widely used forms of woven wire are the dutch or
hollander weaves, wherein the warp and weft are of different diameter, generally
with a corresponding difference in the relative numbers of warp and weft wires. If
the warp wires (i.e. those along the length of the loom) are thicker, the result is
the 'plain dutch weave' of Figure 6.3: the alternative is for the weft wires (across
the loom) to be the thicker, giving the 'reverse plain dutch weave' of Figure 6.4.
'Plain dutch weave' is also known as single plain dutch weave, basket weave,
reps and corduroy. It forms a filter cloth that is easy to clean and has a low
resistance to flow, but is of limited strength. 'Reverse plain dutch weave' is
substantially stronger, and is in fact the strongest filter weave in commercial
production; as a result, coupled with its good flow characteristics and high dirt-
holding capacity, it is widely used industrially.
By a similar combination of warp and weft wires of different diameters, two
basic forms of twilled dutch weave are produced. The use of heavy warp wires
results in 'dutch twilled weave' (Figure 6.5), which permits the production of the
very finest grades of woven wire cloths, while also having the advantage of a
very smooth surface on both sides: its disadvantage is a relatively high resistance
to flow. With heavy weft wires, 'twilled reverse dutch weave' is formed (Figure
6.6); this offers less resistance to flow but with a corresponding decrease in
micron retention characteristics and with rough surfaces on both sides.
Numerous variations exist around these basic weaves. Thus the Haver and
Boecker range of wire cloths includes not only the four dutch weaves described
above, but also 'broad mesh twilled dutch weave' in which the weft wires are not
arranged to give a 'light-tight' cloth but have a preset spacing between them:
because of this, the weft mesh count and the retention vary somewhat at intervals.
Their patented Zig-Zag weave uses the same weave but involves a special sequence,
which guarantees the highest possible accuracy and regularity of spacing.
Another variation is to use twisted bundles of fine wires in place of a single
wire. This is particularly favoured in the manufacture of the wire belts that form
the heart of papermaking machines. One version is 'twisted plain weave', with
Table 6.8 Tolerance of aperture sizes of Bopp square-mesh wire cloths
Aperture sizes (lam) ( mm ) Average tolerance of
apertures (o/,,)
2-25 0.020-0.025 + 7.5
32 0.032 _____6.5
36-40 0.036-0.040 +__ 5
55-67 0.056-0.067 +__4.5
71-95 0.071-0.095 +-4
100-170 0.100-0.170 + 3.5
189-400 O. 180-0.400 + 3
425-1600 0.425-1.600 +-2.5