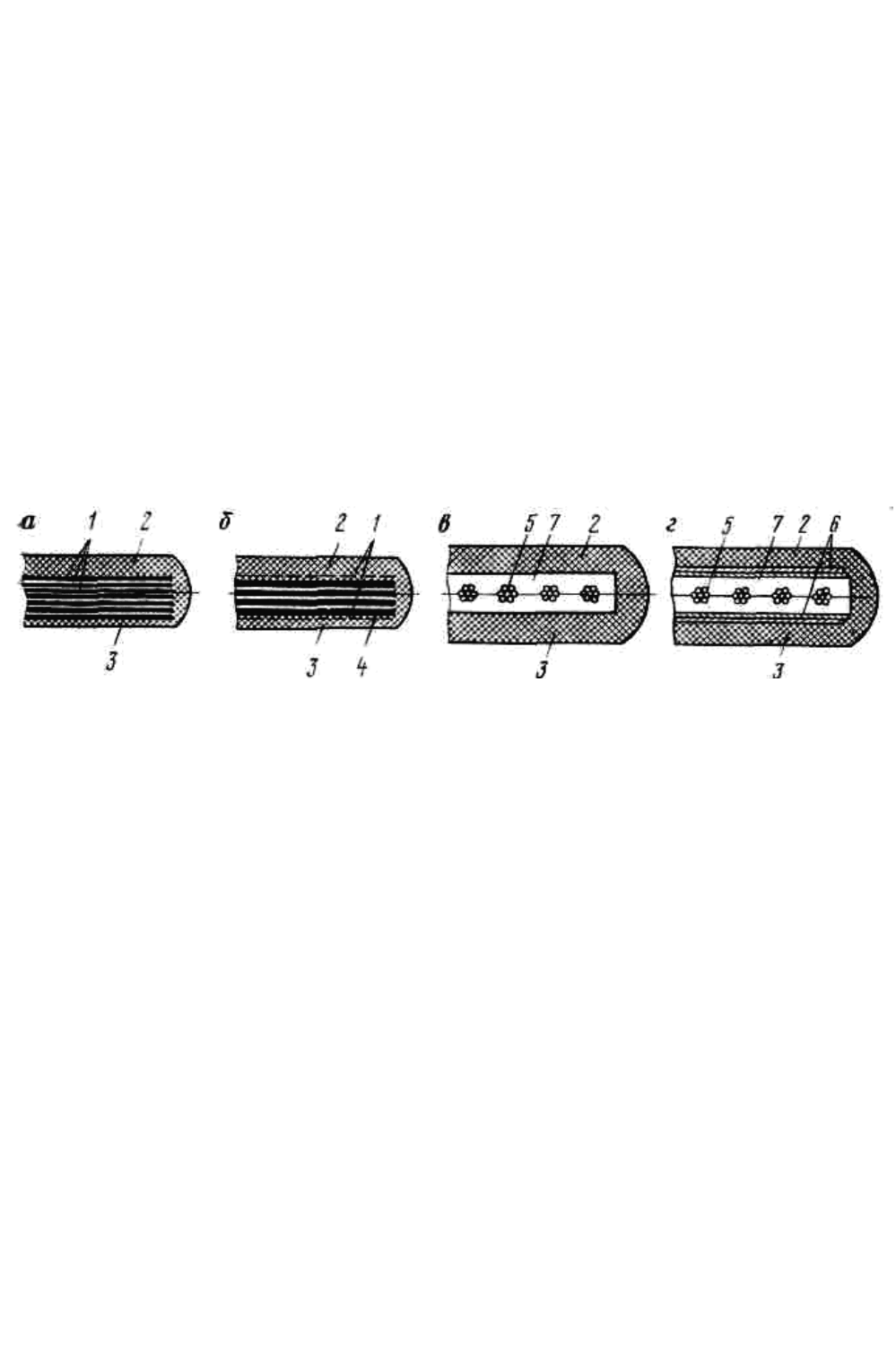
Величину е
μα
называют обычно тяговым фактором. Чем: больше тяговый фактор, тем
большее тяговое усилие развивает привод. Увеличение тягового фактора возможно путем
повышения коэффициента трения μ (например, футеровкой поверхности приводного барабана
резиной) и угла обхвата α (например, при установке двух приводных барабанов с суммарным
расчетным углом обхвата α = α
1
+ α
2
. где α
1
и α
2
— углы обхвата барабанов привода лентой).
Применяют ленточные конвейеры с двухбарабанным приводом с S-образной запасовкой
ленты на барабанах (рис. 15.1, в), когда один барабан привода огибается рабочей (грязной)
стороной ленты, а другой — нерабочей (чистой) стороной, и ленточные конвейеры с двумя
приводными барабанами, огибаемыми лентой только с чистой стороны (рис. 15.1, г). Возможна
установка трех приводных барабанов: два в головной части и один в хвостовой.
15.2. Основные сборочные единицы ленточных конвейеров
Основными сборочными единицами ленточного конвейера являются лента,
роликоопоры и став, приводная станция, натяжное устройство, загрузочное устройство,
очистные устройства и ловители ленты.
Лента является наиболее дорогостоящим и ответственным элементом конвейера.
Стоимость ее составляет 50% от стоимости конвейера, а иногда и более. Лента состоит из
каркаса, передающего тяговые усилия, верхних и нижних обкладок и бортов, предохраняющих
каркас ленты от механических повреждений и проникновения влаги. В отечественной горно-
добывающей промышленности наиболее широко применяют многопрокладочные
резинотканевые (рис. 15.2, а, б) и резинотросовые (рис. 15.2, в, г) ленты.
Рис. 15.2. Конструкция конвейерных лент: 1 — прокладки; 2 — верхняя рабочая обкладка; 3 — нижняя обкладка; 4
— брекерная ткань; 5 — трос; 6 — предохранительная прокладка; 7 — резиновый наполнитель
Для шахтных подземных конвейеров используют многопрокладочные ленты (табл. 15.1).
Каркас этих лент состоит из ряда тканевых прокладок, между которыми расположен тонкий
слой резины (сквидж) толщиной 0,2—0,3 мм. Нити тканевых прокладок, направленные вдоль
ленты и воспринимающие тяговые усилия, называются основными, а поперек — уточными,
служащими для придания ленте поперечной жесткости. Прокладки со всех сторон защищены
огнестойкой резиной. Толщина верхней обкладки составляет 6—10 мм, нижней — 2÷3,5 мм.
В многопрокладочных лентах, предназначенных для транспортирования
крупнокусковых скальных грузов, под верхней обкладкой располагают защитную (брекерную)
прокладку (см. рис. 15.2, б), обеспечивающую предохранение от пробоя прокладок каркаса
крупными кусками и увеличивающую прочность связи верхней рабочей обкладки с
прокладками каркаса.
Тканевые прокладки отечественных лент изготавливают из комбинированных тканей
(полиэфир/хлопок) типа БКНЛ-65 прочностью по основе 65 Н/мм ширины одной прокладки, а
также на основе синтетических полиамидных волокон прочностью на разрыв 100—400 Н/мм
(типа ТА-100, ТК-200, ТА-400, ТК-400 и др.). Число прокладок в ленте i = l÷6, прочность ткани
прокладки по утку составляет 30—40% от прочности по основе.
Разрывное усилие (Н) многопрокладочной ленты S
раз
шириной В (мм) с числом
прокладок i
S
раз
= Bσi
где σ — прочность на разрыв одной прокладки, Н/мм ширины прокладки.
Недостаток ленты из синтетических тканей — удлинение при рабочих нагрузках до 3—
3,5%.
Пример условного обозначения многопрокладочной ленты конвейерного типа 1, подтипа
2Ш, трудновоспламеняющейся для шахтных условий, шириной 1000 мм, с пятью прокладками
из ткани ТК-200, с рабочей обкладкой толщиной 6 мм и нерабочей 3,5 мм из резины класса Г-1:
ленты 1.2Ш×1000×5×ТК-200×6-3,5×Г-1 ГОСТ 20—85.