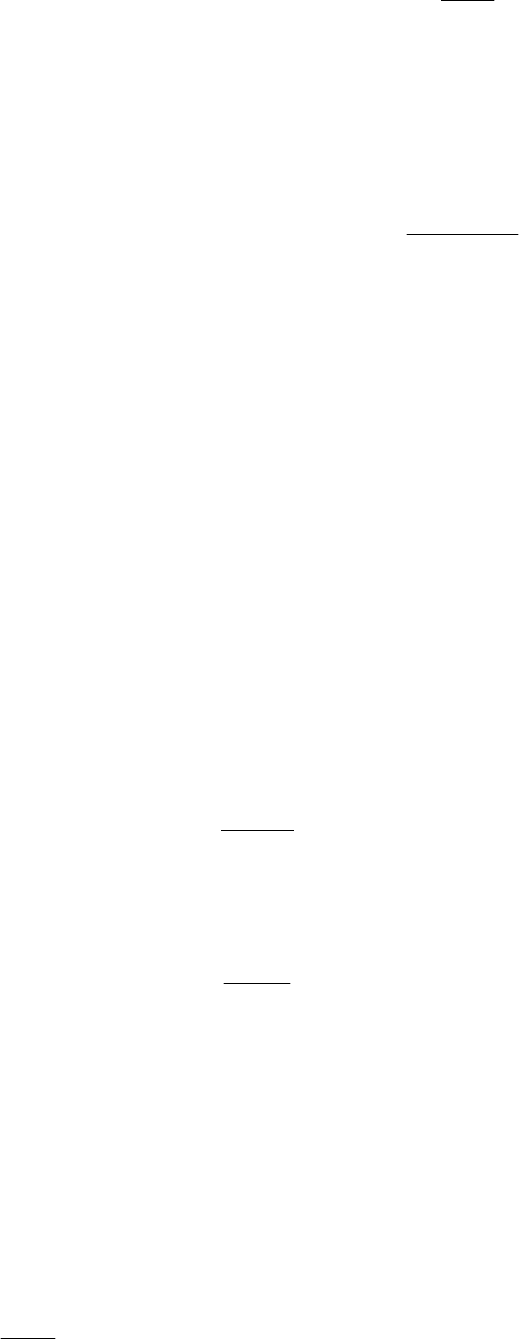
Расчет количества транспортных устройств и их загрузки. Количество транспортных устройств периодического
действия: штабелеров, электропогрузчиков, робокар – для выполнения операций на складах определяют по формуле
ид
нc
шт
Ф K
KT
N
Σ
= , (4.41)
где Т
с∑
– суммарное время работы штабелера для перемещения месячного объема заготовок, ч; Ф
д
– месячный фонд времени
работы штабелера. Принимается для двухсменной работы Ф
д
= 305 ч и Ф
д
= 381 – для трехсменной работы; K
н
– коэффици-
ент, учитывающий неравномерность поступления (
K
н
= 1,3) и отпуска (K
н
= 1,5) грузов; K
и
– коэффициент использования
транспортного средства, принимаемый равным 0,8.
Суммарное время транспортных операций на перемещение месячного объема груза транспортом данного вида
Ι
=
Σ
∑
=
т
1
т.отц
c
60Z
KZT
T
m
i
i
, (4.42)
где
ц
T – средняя продолжительность одного транспортного цикла, мин;
∑
=
m
i
i
Z
1
т
– суммарное количество перемещений
транспорта по перевозке груза (числа поддонов
i
Z
т
по m видов груза) в течение месяца;
т.о
K - число транспортных операций
в технологическом процессе изготовления детали;
Ι
т
Z
– число поддонов (объем груза), перемещаемых транспортом за один
цикл.
Суммарное время работы штабелера для перемещения месячного объема заготовок (числа поддонов) можно определить
по ранее приведенной формуле (2.10) при рассмотрении примера расчета штабелеров ГПС обработки корпусных деталей:
)(
стстстстстстелстстелc −−−−Σ
= KТKTT ,
где
стстел−
T и
стст−
Т – среднестатистическое значение времени одного перемещения штабелера от стеллажа склада к станку и
между станками, соответственно, мин;
стстел−
K и
стст−
K – суммарное значение этих перемещений в течение месяца.
При определении числа транспортных операций следует иметь в виду, что штабелер при одноадресном цикле работы
(склад – станок – склад) совершает два перемещения: сначала к операционному накопителю станка, затем обратно к складу;
при двухадресном цикле (склад – станок – разгрузочная площадка) – одно перемещение.
Средняя длительность цикла одного перемещения зависит от скорости перемещения штабелера (табл. 4.4, 4.7), числа
секций и ярусов хранения, и для 30…50-секционных складов при одноадресном цикле работа штабелера составляет
ц
T =
1,2…1,6 мин [5, c. 157].
Расчет числа позиций контроля автоматизированного склада. Структура расчета числа позиций контроля анало-
гична расчету позиций контроля ГПС обработки корпусных деталей (формула (2.7)):
60Ф
поз
дет.кк
поз.к
⋅
=
Σ
kt
n
,
где
Σк
t – суммарное время контроля одной деталеустановки, мин;
дет.к
k
– число деталей, проходящих выборочный контроль
в течение месяца;
поз
Ф – месячный фонд времени работы позиций контроля, ч.
Число деталеустановок, проходящих выборочный контроль (формула (2.8))
n
nk
k
мнаим
дет.к
= ,
где n = 5…8 деталей – норматив выборочного контроля.
Суммарное время контроля при токарной обработке одной детали
Σк
t , обрабатываемой на станочном комплексе за две
установки (две операции), состоит из одного операционного контроля и одного послеоперационного (окончательного) кон-
троля, совмещенного со второй операцией, т.е.
о.к1к
ttt
Σ
.
Время межоперационного контроля в расчетах можно принимать равным t
1
= 5 мин, время окончательного контроля t
о.к
= 8 мин.
Пример выбора и расчета оборудования станочного комплекса и оборудования АТСС. Исходные данные.
Класс детали – втулка (табл. П3).
Годовой объем выпуска деталей в ГПС –
N
г
= 16 800 шт.
Сведения о детали-представителе:
– конструктивные размеры – по чертежу рис. 4.1;
– годовой объем выпуска
480
35
80016
г
==n шт.;
– наибольшие габаритные размеры
D × L = 80 × 90 мм;
– масса заготовки 0,5 кг.
Маршрутный технологический процесс: