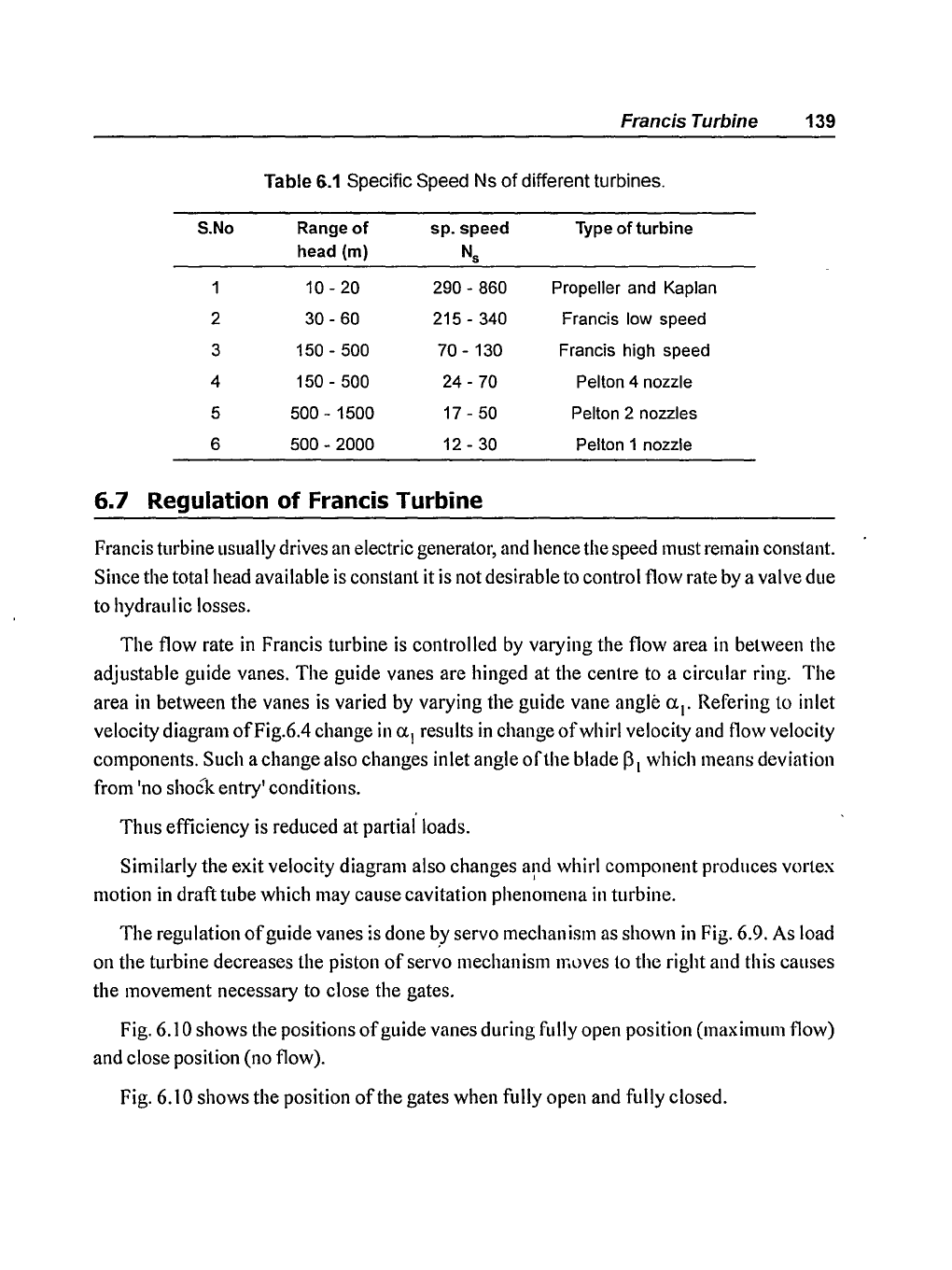
Francis Turbine 139
Table
6.1
Specific Speed Ns
of
different turbines.
S.No
Range
of
sp.speed
Type
ofturbine
head (m)
Ns
1 10 - 20 290 - 860 Propeller and Kaplan
2
30 - 60 215 - 340 Francis low speed
3
150 - 500 70 - 130 Francis high speed
4
150 - 500 24 - 70 Pelton 4 nozzle
5
500 - 1500
17 - 50 Pelton 2 nozzles
6
500 - 2000 12 - 30 Pelton 1 nozzle
6.7 Regulation of Francis Turbine
Francis turbine usually drives an electric generator, and hence the speed must remain constant.
Since the total head available
is
constant it is not desirable to control flow rate by a valve due
to hydraulic losses.
The
flow rate
in
Francis turbine
is
controlled
by
varying the flow area
in
between the
adjustable guide vanes.
The
guide vanes are hinged
at
the centre to a circular ring.
The
area
in
between the vanes is varied by varying the guide vane angle u
1
•
Refering to inlet
velocity diagram ofFig.6.4 change
in
u
1
results
in
change
of
whirl velocity and flow velocity
components. Such a change also changes inlet angle
of
the blade
[31
which means deviation
from 'no
shock entry' conditions.
Thus efficiency is reduced at partial loads.
Similarly the exit velocity diagram also changes and whirl component produces vortex
I
motion
in
draft tube which may cause cavitation phenomena
in
turbine.
The
regulation
of
guide vanes is done by servo mechanism as shown
in
Fig. 6.9. As load
on the turbine decreases the piston
of
servo mechanism
Ir,l>ves
to the right and this causes
the movement necessary to close the gates.
Fig.
6.10 shows the positions
of
guide vanes during fully open position (maximum flow)
and close position (no flow).
Fig.
6.10 shows the position
of
the gates when fully open and fulIy closed.