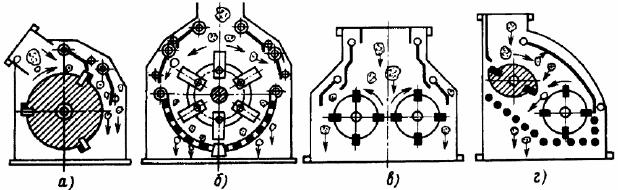
В измельчителях ударного действия измельчение материала осущест-
вляется под действием ударных нагрузок, которые могут возникать при
взаимном столкновении частиц измельчаемого материала, столкновении
частиц материала с неподвижной поверхностью, столкновении материала и
движущихся рабочих органов машин.
К дробилкам ударного действия относятся роторные и молотковые
дробилки, а также пальцевые измельчители.
В дробилках ударного действия кусок подвергается воздействию ра-
бочего органа только с одной стороны. Возникающая при этом сила урав-
новешивается силой инерции куска, которая должна быть достаточной для
создания разрушающих напряжений. Дробление материала происходит под
воздействием механического удара. При этом кинетическая энергия дви-
жущихся тел частично или полностью переходит в деформации разруше-
ния.
Дробилки ударного действия применяют для измельчения малоабра-
зивных материалов средней и низкой прочности (известняков, мела, гипса,
калийных руд и др.). Они обеспечивают высокую степень измельчения i =
15…20, в отдельных случаях до i = 50, что позволяет уменьшить число ста-
дий дробления. Дробилки отличаются простотой конструкции и эксплуата-
ции, избирательностью дробления и малой металлоемкостью.
Рис. 1.14. Принципиальные схемы ударных дробилок
По конструкции рабочих органов дробилки ударного действия делят
на роторные с жестко закрепленными билами (рис. 1.14, а, в, г), молотко-
вые с шарнирно подвешенными молотками (рис. 1.14, б) и пальцевые из-
мельчители.
По числу роторов различают однороторные (рис. 1.14, а) и двухротор-
ные (рис. 1.14, в, г) дробилки. Двухроторные дробилки одноступенчатого
дробления (рис. 1.14, в) имеют высокую производительность. Исходный
материал поступает равномерно на оба ротора, которые работают само-
стоятельно в одном корпусе. В двухроторных дробилках двухступенчатого
дробления (рис. 1.14, г) материал в зоне действия первого ротора подверга-
ется предварительному дроблению, а затем в зоне действия второго ротора
– повторному дроблению.
Роторные дробилки могут применяться для дробления крупных кус-
ков, так как имеют массивный ротор и обладают большим запасом энергии
рабочих органов.
В молотковых дробилках (рис. 1.14, б) процесс дробления определяет
лишь кинетическая энергия самого молотка.
В пальцевых измельчителях рабочим органом являются два диска с
установленными по их периферии пальцами. Различают пальцевые измель-
чители с одним вращающимся диском (дисмембраторы) и с двумя вра-
щающимися навстречу друг другу дисками (дезинтеграторы).
Типоразмеры роторных и молотковых дробилок определяются диа-
метром и длиной ротора, а пальцевых измельчителей – наружным диамет-
ром диска.
По технологическому назначению роторные дробилки делят на дро-
билки крупного (ДРК), среднего (ДРС) и мелкого дробления (ДРМ). Прин-
ципиальные конструктивные схемы роторных дробилок во многом одина-
ковы и отличаются числом отражательных плит и соотношениями размеров
ротора. Камера дробления у дробилок ДРК образуется ротором и двумя
отражательными плитами, у дробилок ДРС и ДРМ – ротором и тремя пли-
тами. Конструкция роторной дробилки для крупного дробления показана
на рис. 1.15. Корпус дробилки – сварной,