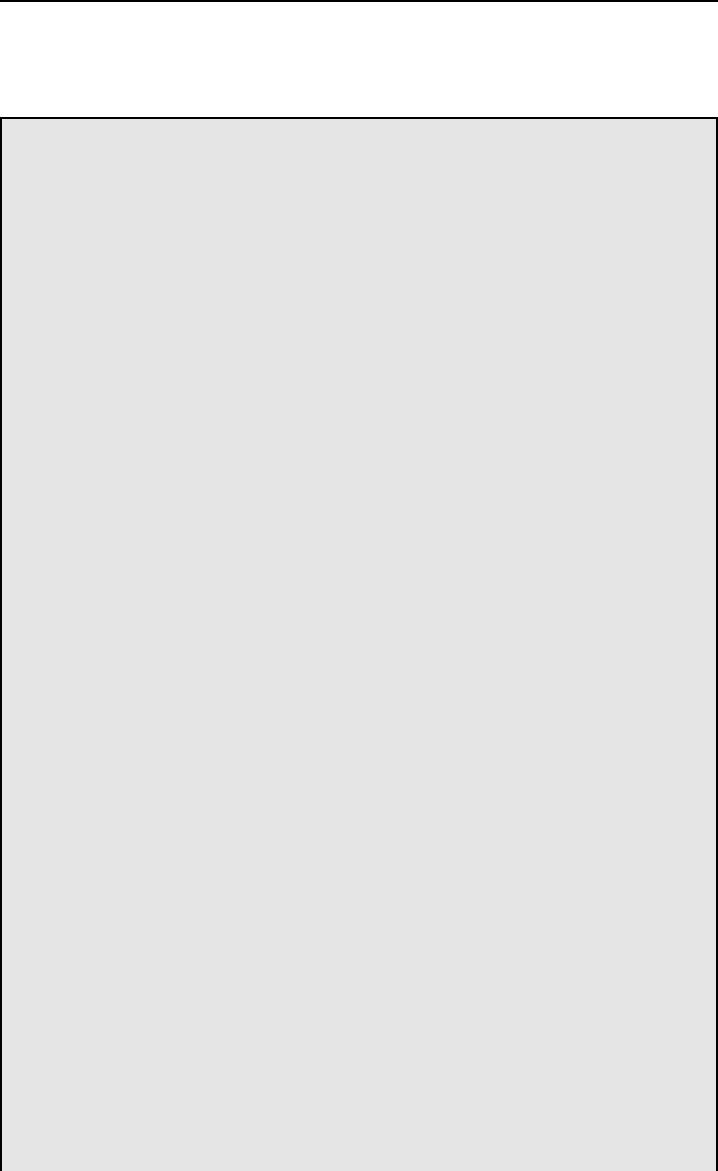
110 HIGH-INVOLVEMENT INNOVATION
• To meet different personal preferences—some people like to work in teams,
others are natural ‘loners’ and prefer a more individual kind of HII vehicle
BOX 6.3 Getting in the driving seat.
The MD and Quality Manager of a medium-sized manufacturing company believed that
continuous improvement would help the company survive the recession and provide an
impetus for tackling several long-standing issues that had started to grow into serious problems
and could no longer be ignored. They understood that high-involvement innovation (HII)
is about involving everyone in the organization and ran a series of awareness seminars,
attended by all employees over a three-month period, at which they explained the concept
of HII and its underlying principles. The MD and Quality Manager identified a number of
‘Champions’ who they saw as being the main conduit for extending HII activity throughout
the organization. The Champions were tasked with encouraging people to look for and
implement improvements, and to give help where it was needed.
There was an initial burst of activity, especially on the shop floor, where the Production
Manager was a very active Champion. Many staff were enthusiastic about the idea of
HII and started to work on improvements, often in small workplace groups. Early successes
started to be featured in the company newsletter.
However, after about six months there was a noticeable drop in improvement activity. The
level of activity in any area depended largely on how active the local champion was and,
in many cases, it was the same handful of people responsible for all the HII going on. By the
end of the year there had only been a small amount of improvement in the big problem issues
the company faced, though other problems had developed. In retrospect, this was attributed
to the
ad hoc
nature of the improvement activity: people worked on whatever they wanted
and this led in some cases to groups with conflicting objectives pulling in opposite directions
to each other, and to the way the company wanted to go. In addition, the informality,
while encouraging spontaneity, had also led to a lot of time being spent in meetings and
discussions that led nowhere, duplication of effort and inconsistency. These factors combined
to leave many people feeling disillusioned with HII and little inclined to continue to take part.
As a result of sharing this experience with his counterparts in other companies and finding
out what they were doing, the Quality Manager drew up a proposal for some formal ‘HII
vehicles’. This was accepted and put into effect during the following year. The vehicles
enabled people to participate in HII activity as individuals and as members of teams. The
system was deliberately kept as unbureaucratic as possible, but the provision of these formal
vehicles quickly brought significant benefits: a much wider range of people became involved
in HII because there were company-wide mechanisms that they could use; and the increased
control over team activity ensured that all the teams worked in the same direction, and in a
way to help achieve the company’s objectives. This stronger focus led to a much improved
ratio of effort to benefits gained, which in turn increased motivation and stimulated repeated
involvement in HII. There were still a few problems—in particular, pockets of little HII activity
and some management resistance—which took time to resolve. Nevertheless, the introduction
of these formal vehicles was a watershed in the development of HII in the company.
In another case, an automotive components company had been running team-oriented HII
vehicles for three years. The vehicles worked well and had brought many benefits, including
significant savings. However, there was a limit to the number of teams that could be up and