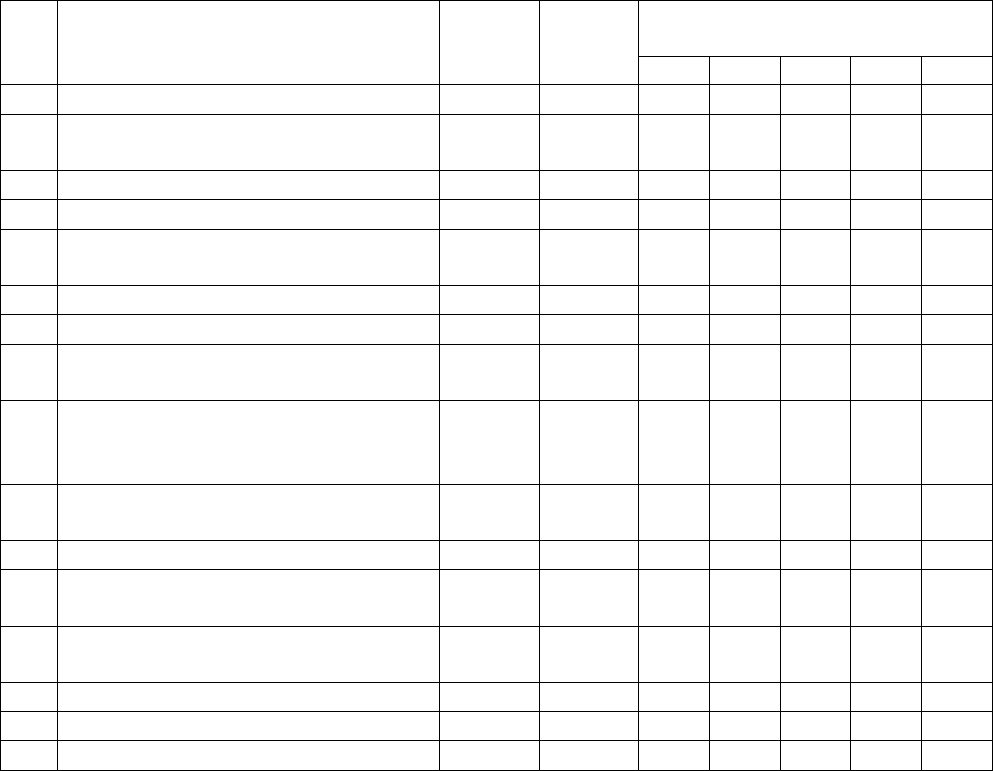
5
гидропневматическую подушку (на рис. 1.а не показана), которая применена
для обеспечения постоянства усилия прессования. Прессование порошка в
матрице происходит при движении ползуна 5 вниз; при этом усилие F
5
прессования изменяется согласно графику на рис. 1б. Перемещение ползуна 5
вверх происходит с меньшей средней скоростью (K
V
< 1). В это время
спрессованное изделие удаляется из матрицы 9 выталкивателем 12,
кинематически связанным с коромыслом 8 кулачкового механизма, кулачок 7
которого установлен на распределительном валу. Затем изделие сталкивается
на ленточный транспортер. Одновременно новая порция порошка поступает из
бункера в шибер и т.д.
Кулачковый механизм выталкивателя обеспечивает заданный на рис. 1в
закон движения коромысла 8. Допустимый угол давления [θ] = 35°.
Исходные данные
таблица 1
Числовые значения для
вариантов
№
п/п
Наименование параметра
Обозна
чение
Единица
СИ
А Б В Г Д
1 Ход ползуна 5
H
5
м 0,06 0,07 0,08 0,09 0,1
2
Коэффициент изменения средней
скорости ползуна 5
K
V
- 0,62 0,6 0,58 0,56 0,54
3 Частота вращения кривошипа 1
n
1
c
–1
0,32 0,34 0,36 0,38 0,4
4 Длина стойки 6
l
6
м 0,3 0,32 0,34 0,35 0,36
5
Максимальное усилие
прессования
F
max
кН 14,0 14,5 15,0 15,5 16,0
6 Вес кулисы 3
G
3
Н 320 350 380 400 420
7 Вес ползуна 5
G
5
Н 420 480 520 580 620
8
Момент инерции кулисы 3
относительно ее центра масс S
3
J
3S
кг·м
2
45 46 68 82 94
9
Момент инерции вращающихся
деталей, приведенный к валу
электродвигателя
J
np
кг·м
2
0,08 0,085 0,09 0,09 0,1
10
Угловая координата кривошипа
(для силового расчета механизма)
φ
1
град 40 50 40 50 40
11 Число зубьев колес
Z
5
; Z
6
- 10;19 11;21 12;23 13;25 14;27
12
Передаточное отношение
планетарного редуктора
U
1h
- 21 19 18 17 16
13
Модуль зубчатых колес
планетарного редуктора
m
I
мм 3 4 3 4 3
14 Угол рабочего профиля кулачка 7
δ
p
град 90 100 110 120 130
15 Длина коромысла 8
l
GK
м 0,18 0,2 0,22 0,18 0,23
16 Угол поворота коромысла 8
φ
8
град 16 15 14 16 12