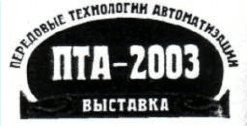
3.6. Некоторые передовые технологии автоматизации
(ПТА) на российских бетонных заводах
Несмотря на имеющиеся сложности в развитии экономики РФ, нам
представляется, что новые передовые технологии автоматизации в
строительной индустрии всё же разрабатываются и внедряются. Так,
например, в статье [54] освещались передовые технологии автоматизации с
9 по 11 декабря 2003 года в Москве в Центре международной торговли во
время выставки «Передовые технологии автоматизации 2003» (ПТА-2003).
Рассмотрим некоторые современные разработки, которые используются на
бетонных заводах с передовой технологией автоматизации и приведем их
кратких технико-экономические характеристик.
Организатором выставки стала выставочная компания
«Экспотроника» при официальной поддержке Российского агентства по
системам управления, Российской инженерной академии, Управления по
атомному машиностроению и приборостроению Минатома РФ,
Российского представительства Общества приборостроения, систем и
автоматики (ISA), Координационного совета по проблемам стандартизации
систем промышленной автоматизации.
ПТА-2003 – это ведущая специализированная выставка оборудования
и технологий для АСУ ТП и встраиваемых систем. Главной целью
выставки является демонстрация передовых технических решений в
области промышленной автоматизации, новинок оборудования и
программного обеспечения, а также услуг по разработке и внедрению
автоматизированных систем.
Среди участников ПТА-2003 были крупнейшие российские и за-
рубежные производители оборудования и программных средств для АСУ
ТП, разработчики аппаратуры и комплексных решений автоматизации в
различных отраслях промышленности, производственно-внедренческие
фирмы, поставщики специализированных компьютеров и промышленной
электроники.
Одновременно с выставкой в конференц-зале ЦМТ прошла Все-
российская конференция по АСУ ТП и встраиваемым системам. Вни-
манию слушателей конференции предлагались доклады ведущих